2024.2.16
Uncovering the Secrets Behind the Silent Flight of Owls
Researchers investigate the aeroacoustic mechanisms that allow owls to fly silently using numerical simulations.
Owls produce negligible noise while flying. While many studies have linked the micro-fringes in owl wings to their silent flight, the exact mechanisms have been unclear. Now, a team of researchers has uncovered the effects of these micro-fringes on the sound and aerodynamic performance of owl wings through computational fluid dynamic simulations. Their findings can inspire biomimetic designs for the development of low-noise fluid machinery.
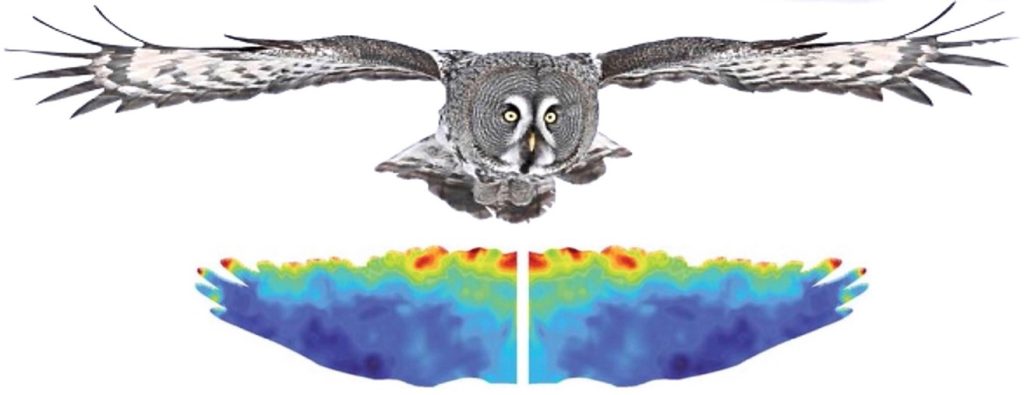
The micro-fringes on owl wings effectively suppress the noise while maintaining the aerodynamic performance of the wings comparable to that of a wing without the fringes.
Credit:Hao Liu from Chiba University, this image cannot be reused without permission.
Research Background
Owls are fascinating creatures that can fly silently through some of the quietest places. Their wings make no noise while flying, enabling them to accurately locate their prey using their exceptional hearing ability while remaining undetected. This unique ability depends on many factors and has long been a hot research subject.
Studies have found associations between the ability to fly silently and the presence of micro-fringes in owl wings. These trailing-edge (TE) fringes play a crucial role in suppressing the noise produced by wing flap-induced air movement.
Studying these fringes can lead to the development of promising methods to reduce noise caused by fluid machinery. While many studies have evaluated these fringes using flat plates and airfoils, their exact mechanisms and effects on the interactions of feathers and the different wing features in real owl wings remained unknown.
When asked about the motivation behind their study, Prof. Liu says, “Despite many efforts by many researchers, exactly how owls achieve silent flight is still an open question. Understanding the precise role of TE fringes in their silent flight will enable us to apply them in developing practical low-noise fluid machinery.” Their findings were published in the journal Bioinspiration & Biomimetics on November 17, 2023.
To understand how owl wings work, the team constructed two three-dimensional models of a real owl wing—one with and the other without TE fringes—with all its geometric characteristics. They used these models to conduct fluid flow simulations that combined the methods of large eddy simulations and the Ffowcs-Williams-Hawkings analogy. The simulations were conducted at the speed of the gliding flight of approach of a real owl.
Simulations revealed that the TE fringes reduced the noise levels of owl wings, particularly at high angles of attack, and maintained aerodynamic performance comparable to owl wings without fringes. The team identified two complementary mechanisms through which the TE fringes influence airflow. First, the fringes reduce the fluctuations in airflow by breaking up the trailing edge vortices. Second, they reduce the flow interactions between feathers at the wingtips, thereby suppressing the shedding of wingtip vortices. Synergistically, these mechanisms enhance the effects of TE fringes, improving both aerodynamic force production and noise reduction.
Emphasizing the significance of these results, Prof. Liu says, “Our findings demonstrate the effect of complex interactions between the TE fringes and the various wing features, highlighting the validity of using these fringes for reducing noise in practical applications such as drones, wind turbines, propellers and even flying cars.”
Overall, this study deepens our understanding of the role of TE fringes in the silent flight of owls and can inspire biomimetic designs that could lead to the development of low-noise fluid machinery.
Studies have found associations between the ability to fly silently and the presence of micro-fringes in owl wings. These trailing-edge (TE) fringes play a crucial role in suppressing the noise produced by wing flap-induced air movement.
Studying these fringes can lead to the development of promising methods to reduce noise caused by fluid machinery. While many studies have evaluated these fringes using flat plates and airfoils, their exact mechanisms and effects on the interactions of feathers and the different wing features in real owl wings remained unknown.
Research Findings
To unravel the secrets of silent owl wings, Professor Hao Liu with his colleagues, including Dr. Jaixin Rong from the Graduate School of Engineering and Dr. Yajun Jiang and Dr. Masashi Murakami from the Graduate School of Science at Chiba University in Japan, investigated how TE fringes influence both the sound and aerodynamic performance of owl wings.When asked about the motivation behind their study, Prof. Liu says, “Despite many efforts by many researchers, exactly how owls achieve silent flight is still an open question. Understanding the precise role of TE fringes in their silent flight will enable us to apply them in developing practical low-noise fluid machinery.” Their findings were published in the journal Bioinspiration & Biomimetics on November 17, 2023.
To understand how owl wings work, the team constructed two three-dimensional models of a real owl wing—one with and the other without TE fringes—with all its geometric characteristics. They used these models to conduct fluid flow simulations that combined the methods of large eddy simulations and the Ffowcs-Williams-Hawkings analogy. The simulations were conducted at the speed of the gliding flight of approach of a real owl.
Simulations revealed that the TE fringes reduced the noise levels of owl wings, particularly at high angles of attack, and maintained aerodynamic performance comparable to owl wings without fringes. The team identified two complementary mechanisms through which the TE fringes influence airflow. First, the fringes reduce the fluctuations in airflow by breaking up the trailing edge vortices. Second, they reduce the flow interactions between feathers at the wingtips, thereby suppressing the shedding of wingtip vortices. Synergistically, these mechanisms enhance the effects of TE fringes, improving both aerodynamic force production and noise reduction.
Emphasizing the significance of these results, Prof. Liu says, “Our findings demonstrate the effect of complex interactions between the TE fringes and the various wing features, highlighting the validity of using these fringes for reducing noise in practical applications such as drones, wind turbines, propellers and even flying cars.”
Overall, this study deepens our understanding of the role of TE fringes in the silent flight of owls and can inspire biomimetic designs that could lead to the development of low-noise fluid machinery.
About Professor Hao Liu
Dr. Hao Liu is a Professor at the Graduate School of Engineering at Chiba University, Japan. Prof. Liu leads the Center for Aerial Intelligent Vehicles at Chiba University. He obtained his Ph.D. from Yokohama National University in 1992. Prof. Liu has over 600 publications and 11,200 citations to his name (Google Scholar). He is one of the world’s top 2% scientists, according to Stanford University (2023). His research interests include biomechanics, biomimetics, and bio-inspired engineering.
Funding
The research received partial funding from a Grant-in-Aid for Scientific Research of KAKENHI, Japan Society for the Promotion of Science (grant no. 19H00750). Mr. Jiaxin Rong received financial support from the Japanese Government MEXT scholarship and the Excellent International Student Scholarship from Chiba University. The authors are also grateful to the Lake Utonai Wildlife Conservation Center for providing the bird wings used in the study.
Reference
Title of original paper:Trailing-edge fringes enable robust aerodynamic force production and noise suppression in an owl wing modelAuthors: Jiaxin Rong1,2, Yajun Jiang3, Yuta Murayama3, Ryoto Ishibashi3, Masashi Murakami4 and Hao Liu1,2
Affiliations: 1Shanghai Jiao Tong University and Chiba University International Cooperative Research Center, People’s Republic of China 2Graduate School of Engineering, Chiba University, Japan 3Graduate School of Science and Engineering, Chiba University 4Graduate School of Science, Chiba University, Japan
Journal: Bioinspiration & Biomimetics
DOI: https://doi.org/10.1088/1748-3190/ad0aa9
Contact Us
Hao LiuGraduate School of Engineering, Chiba University
Email: hliu@faculty.chiba-u.jp